ફીડ પેલેટ મશીનની ગ્રાન્યુલેશન પ્રક્રિયા દરમિયાન, વ્યક્તિગત ફીડ પેલેટ્સ અથવા વિવિધ રંગોવાળા વ્યક્તિગત ફીડ પેલેટ્સ હોય છે, જેને સામાન્ય રીતે "ફ્લાવર ફીડ" તરીકે ઓળખવામાં આવે છે. આ પરિસ્થિતિ જળચર ફીડના ઉત્પાદનમાં સામાન્ય છે, જે મુખ્યત્વે રિંગ ડાઇમાંથી બહાર કાઢવામાં આવેલા વ્યક્તિગત કણોનો રંગ અન્ય સામાન્ય કણો કરતાં ઘાટો અથવા હળવો હોવા અથવા વ્યક્તિગત કણોની સપાટીનો રંગ અસંગત હોવા તરીકે પ્રગટ થાય છે, જેનાથી ફીડના સમગ્ર બેચના દેખાવની ગુણવત્તા પર અસર પડે છે.
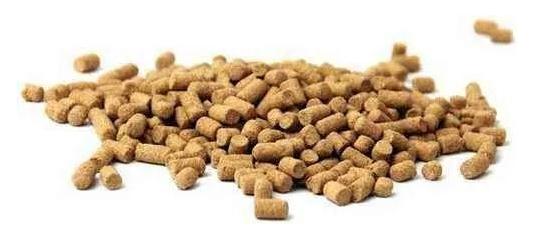
આ ઘટનાના મુખ્ય કારણો નીચે મુજબ છે:
a)ફીડ કાચા માલની રચના ખૂબ જટિલ છે, જેમાં ઘણા બધા પ્રકારના કાચા માલ, અસમાન મિશ્રણ અને ફીડ કણોની પ્રક્રિયા કરતા પહેલા પાવડરમાં અસંગત ભેજનું પ્રમાણ હોય છે.
b)દાણાદાર બનાવવા માટે વપરાતા કાચા માલમાં ભેજનું પ્રમાણ અસંગત હોય છે. જળચર ખોરાકની ઉત્પાદન પ્રક્રિયામાં, અલ્ટ્રાફાઇન ક્રશિંગ પછી કાચા માલમાં પાણીની ખોટને ભરપાઈ કરવા માટે ઘણીવાર મિક્સરમાં થોડી માત્રામાં પાણી ઉમેરવું જરૂરી હોય છે. મિશ્રણ કર્યા પછી, તેને ટેમ્પરિંગ માટે કંડિશનરમાં મોકલવામાં આવે છે. કેટલાક ફીડ ઉત્પાદકો ફીડ બનાવવા માટે ખૂબ જ સરળ પ્રક્રિયાનો ઉપયોગ કરે છે - ફોર્મ્યુલા માટે જરૂરી સામગ્રીને સીધા મિક્સરમાં નાખો અને પૂરતું પાણી ઉમેરો, વ્યાવસાયિક આવશ્યકતાઓ અનુસાર વિગતવાર અને ધીમી ઉમેરવાની પ્રક્રિયા હાથ ધરવાને બદલે. તેથી, તેમને પાણીમાં દ્રાવ્યતાના સંદર્ભમાં ફીડ ઘટકોનું સંતુલિત વિતરણ સુનિશ્ચિત કરવું મુશ્કેલ લાગે છે. જ્યારે આપણે કન્ડીશનીંગ ટ્રીટમેન્ટ માટે આ મિશ્ર ઘટકોનો ઉપયોગ કરીએ છીએ, ત્યારે આપણે શોધીશું કે કંડિશનરની કાર્યક્ષમતાને કારણે, ભેજનું પ્રમાણ ઝડપથી સમાન રીતે વિખેરી શકાતું નથી. તેથી, વરાળની ક્રિયા હેઠળ પ્રોસેસ્ડ ફીડ ઉત્પાદનોની પરિપક્વતા વિવિધ ભાગોમાં મોટા પ્રમાણમાં બદલાય છે, અને દાણાદાર બનાવ્યા પછી રંગ વંશવેલો પૂરતો સ્પષ્ટ થતો નથી.
c)ગ્રાન્યુલેશન બિનમાં વારંવાર ગ્રાન્યુલેશન સાથે રિસાયકલ કરેલી સામગ્રી હોય છે. ગ્રાન્યુલેશન પછી દાણાદાર સામગ્રીને ઠંડુ અને સ્ક્રીનીંગ કર્યા પછી જ તૈયાર ઉત્પાદનમાં બદલી શકાય છે. સ્ક્રીનીંગ કરેલ બારીક પાવડર અથવા નાના કણોની સામગ્રી ઘણીવાર ફરીથી ગ્રાન્યુલેશન માટે ઉત્પાદન પ્રક્રિયામાં પ્રવેશ કરે છે, સામાન્ય રીતે મિક્સરમાં અથવા ગ્રાન્યુલેશન સાયલોની રાહ જોતા. આ પ્રકારની રીટર્ન સામગ્રી ફરીથી કન્ડિશન્ડ અને ગ્રાન્યુલેટેડ હોવાને કારણે, જો તેને અન્ય સહાયક સામગ્રી સાથે અસમાન રીતે મિશ્રિત કરવામાં આવે અથવા કન્ડીશનીંગ પછી રીટર્ન મશીન નાના કણોની સામગ્રી સાથે મિશ્રિત કરવામાં આવે, તો તે ક્યારેક ચોક્કસ ફીડ ફોર્મ્યુલા માટે "ફૂલ સામગ્રી" ઉત્પન્ન કરી શકે છે.
d)રિંગ ડાઇ એપરચરની આંતરિક દિવાલની સુગમતા અસંગત છે. ડાઇ હોલની સપાટીની પૂર્ણાહુતિ અસંગત હોવાને કારણે, એક્સટ્રુઝન દરમિયાન પદાર્થ જે પ્રતિકાર અને એક્સટ્રુઝન દબાણનો અનુભવ કરે છે તે અલગ હોય છે, જેના પરિણામે રંગમાં અસંગત ફેરફાર થાય છે. વધુમાં, કેટલાક રિંગ ડાઇમાં નાના છિદ્રની દિવાલો પર બર હોય છે, જે એક્સટ્રુઝન દરમિયાન કણોની સપાટીને ખંજવાળી શકે છે, જેના પરિણામે વ્યક્તિગત કણો માટે સપાટીના રંગો અલગ અલગ હોય છે.
ઉપર સૂચિબદ્ધ "ફૂલ સામગ્રી" ઉત્પન્ન કરવાના ચાર કારણો માટે સુધારણા પદ્ધતિઓ પહેલાથી જ ખૂબ જ સ્પષ્ટ છે, મુખ્યત્વે ફોર્મ્યુલામાં દરેક ઘટકની મિશ્રણ એકરૂપતા અને ઉમેરાયેલા પાણીના મિશ્રણ એકરૂપતાને નિયંત્રિત કરવા; ક્વેન્ચિંગ અને ટેમ્પરિંગ કામગીરીમાં સુધારો કરવાથી રંગ ફેરફારો ઘટાડી શકાય છે; રીટર્ન મશીન સામગ્રીને નિયંત્રિત કરો. "ફ્લાવર સામગ્રી" ઉત્પન્ન કરવાની સંભાવના ધરાવતા ફોર્મ્યુલા માટે, રીટર્ન મશીન સામગ્રીને સીધા દાણાદાર ન કરવાનો પ્રયાસ કરો. રીટર્ન મશીન સામગ્રીને કાચા માલ સાથે મિશ્રિત કરવી જોઈએ અને ફરીથી કચડી નાખવી જોઈએ; ડાઇ છિદ્રોની સરળતાને નિયંત્રિત કરવા માટે ઉચ્ચ-ગુણવત્તાવાળા રિંગ ડાઇનો ઉપયોગ કરો, અને જો જરૂરી હોય તો, ઉપયોગ કરતા પહેલા રિંગ ડાઇ છિદ્રોને પીસી લો.
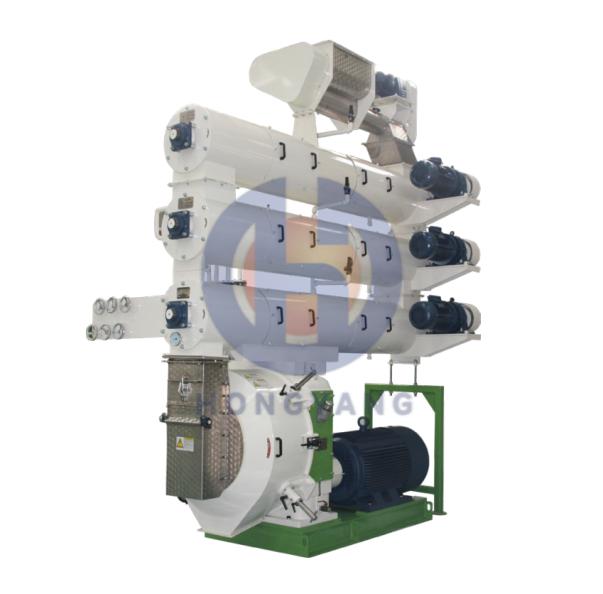
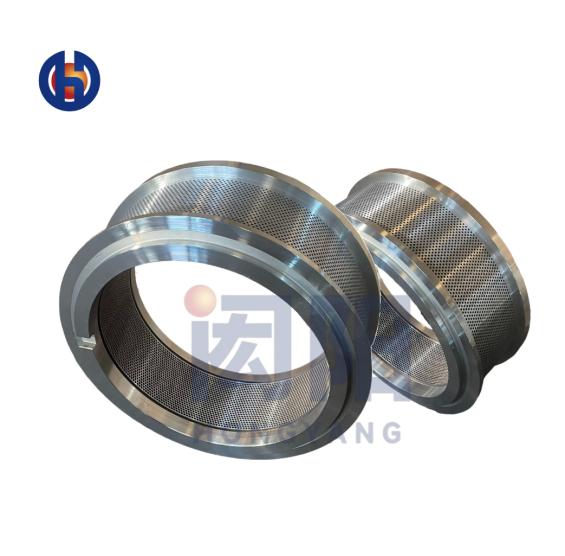
બે-સ્તરવાળા ડ્યુઅલ એક્સિસ ડિફરન્શિયલ કન્ડિશનર અને બે-સ્તરવાળા એક્સટેન્ડેડ જેકેટ કન્ડિશનરને ગોઠવવાની ભલામણ કરવામાં આવે છે, જેનો ક્વેન્ચિંગ સમય 60-120 સેકન્ડ સુધીનો હોય અને 100 ℃ થી વધુ તાપમાન ક્વેન્ચિંગ હોય. ક્વેન્ચિંગ એકસમાન હોય છે અને કામગીરી ઉત્તમ હોય છે. મલ્ટી-પોઇન્ટ એર ઇન્ટેકનો ઉપયોગ સામગ્રી અને સ્ટીમના ક્રોસ-સેક્શનલ એરિયામાં ઘણો વધારો કરે છે, જેનાથી સામગ્રીની પરિપક્વતામાં સુધારો થાય છે અને ક્વેન્ચિંગ અને ટેમ્પરિંગ અસરમાં સુધારો થાય છે; ડિજિટલ ઇન્સ્ટ્રુમેન્ટ પેનલ અને તાપમાન સેન્સર કન્ડીશનીંગનું તાપમાન પ્રદર્શિત કરી શકે છે, જેનાથી વપરાશકર્તાઓ માટે કોઈપણ સમયે નિયંત્રણ કરવાનું સરળ બને છે.
ટેકનિકલ સપોર્ટ સંપર્ક માહિતી:
વોટ્સએપ : +8618912316448
ઈ-મેલ:hongyangringdie@outlook.com
પોસ્ટ સમય: જુલાઈ-26-2023